Published Thursday, 31 May, 2007 at 01:23 PM
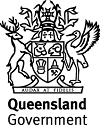
JOINT STATEMENT
Premier and Minister for Trade
The Honourable Peter Beattie
Deputy Premier, Treasurer and Minister for Infrastructure
The Honourable Anna Bligh
PREMIER DIGS DEEP FOR DESAL
TUGUN: Premier Peter Beattie and Deputy Premier Anna Bligh today unveiled the first of two giant tunnel boring machines (TBMs) that will be used to excavate the marine intake and outlet tunnels for the $1.2 billion Gold Coast Desalination Project.
The giant three metre-wide machines feature a series of rotating cutters that enable them to excavate 75 metres of tunnel every week through solid bedrock.
When fully assembled, the purpose-built German-made machines will weigh 150 tonnes and be 71m long.
Mr Beattie today viewed the 70 metre-deep intake and outlet tunnels, and the pre-treatment and reverse osmosis buildings currently under construction.
“The construction process of this project is very impressive,” Mr Beattie said.
“It is employing the most advanced water pre-treatment, reverse osmosis and tunnelling technology available in the world today.
“This critical infrastructure project is one of a number of initiatives the Government is undertaking to drought proof South East Queensland.
“Nearly 700 workers are now on site, with those on actual tunnelling working 24/7 to make this happen.
“It has attracted expertise from around the globe. Over 20 nationalities are employed on the project and some of the world’s best tunnelling and desalination experts are now working to deliver fresh water to South East Queensland,” he said.
Ms Bligh said the Gold Coast project had a number benefits over similar projects elsewhere in Australia and internationally.
“A great benefit of the Tugun site is that unlike Sydney and other places, this is a marine tunnelling program, having minimal impact on the environment and local communities as the tunnels - which will be 70m underground - do not run under any privately-owned land.
“The other great benefit, unlike many desal plants in the Middle East is that the water we are desalinating has lower natural salinity than many other plants.
“We are also operating in deeper water than most, including Western Australia, and have a large marine mass in the Pacific Ocean, plus the benefit of strong tidal currents to help disperse the outfall.
“All of this works with the construction company in delivering this project on-time,” she said.
Ms Bligh said today’s Queensland Water Commission monthly report had the Tugun desalination project on target to meet its regulated dates.
“As scheduled, the desalination project will deliver 125 mega litres of water a day - beginning in November 2008,” she said.
ENDS
Tunnel Boring Machines (TBMs) Fast Facts
• Two purpose built, highly specilialised Tunnel Boring Machines (TBMs) imported from Germany will excavate marine intake and outlet tunnels.
• Each $10m TBM weighs 150 tonnes, is 71m long and propelled by hydraulic rams.
• 300-tonne cranes will lower TBMs into the 70m deep intake and access shafts that are used to access the tunnels.
• All TBMs have a round, rotating cutter head on the front face which is covered in disk cutters (like giant teeth). As the head spins, the ‘teeth’ cut into the rock. The rock is crushed and mixed with a naturally occurring lubricant, bentonite clay, to form slurry. It is then pumped via pipelines within the tunnel back to the plant site.
• Each TBM will excavate about 75m of tunnel every week and about 52,000 cubic metres of material will be excavated – equivalent to 50 Olympic-sized pools.
• The TBMs follow a precise route - guided by GPS that follows a survey grid.
• TBMs used because of minimal impact on 1) environment and 2) local community compared to other tunnelling methods i.e. trenching or above ground piping.
• The tunnels will be excavated 70 metres underground (equivalent to a 20-storey building) through solid bedrock.
• Intake tunnel will be 2.2kms long (750m from the plant to the beach at Tugun, then 1.4kms from the beach out to sea, where it will connect to a marine riser, 20 metres below the surface).
• The outlet tunnel will be 2km long (780m from the plant to the beach at Tugun, then 1.2km from the beach out to sea.
• TBMs will not be excavating under any private property as the tunnel route is under public land. It is also highly unlikely that there will be any sound or vibration generated by the TBMs on the surface due to the depth they will be operating
• Six to eight people will be in each TBM at any one time when operational.
• As TBMs excavate, another highly experienced work team will line the tunnels with specially constructed concrete segments. Six segments are slotted together to form a complete ring.
• A total of 21,000 segments will be used to line the two tunnels.
• Tunnels - internal diameter of 2.8m - external diameter of 3.4m with a 0.2m gap between the concrete segments and the tunnel wall. This will be filled with grout.
• At the completion of the project 80% of the TBMs will be recovered from the tunnel shafts.
Thursday, 31 May 2007
Media contact: 3224 4500 (Premier’s office) 3224 4379 (Deputy Premier’s office)
The giant three metre-wide machines feature a series of rotating cutters that enable them to excavate 75 metres of tunnel every week through solid bedrock.
When fully assembled, the purpose-built German-made machines will weigh 150 tonnes and be 71m long.
Mr Beattie today viewed the 70 metre-deep intake and outlet tunnels, and the pre-treatment and reverse osmosis buildings currently under construction.
“The construction process of this project is very impressive,” Mr Beattie said.
“It is employing the most advanced water pre-treatment, reverse osmosis and tunnelling technology available in the world today.
“This critical infrastructure project is one of a number of initiatives the Government is undertaking to drought proof South East Queensland.
“Nearly 700 workers are now on site, with those on actual tunnelling working 24/7 to make this happen.
“It has attracted expertise from around the globe. Over 20 nationalities are employed on the project and some of the world’s best tunnelling and desalination experts are now working to deliver fresh water to South East Queensland,” he said.
Ms Bligh said the Gold Coast project had a number benefits over similar projects elsewhere in Australia and internationally.
“A great benefit of the Tugun site is that unlike Sydney and other places, this is a marine tunnelling program, having minimal impact on the environment and local communities as the tunnels - which will be 70m underground - do not run under any privately-owned land.
“The other great benefit, unlike many desal plants in the Middle East is that the water we are desalinating has lower natural salinity than many other plants.
“We are also operating in deeper water than most, including Western Australia, and have a large marine mass in the Pacific Ocean, plus the benefit of strong tidal currents to help disperse the outfall.
“All of this works with the construction company in delivering this project on-time,” she said.
Ms Bligh said today’s Queensland Water Commission monthly report had the Tugun desalination project on target to meet its regulated dates.
“As scheduled, the desalination project will deliver 125 mega litres of water a day - beginning in November 2008,” she said.
ENDS
Tunnel Boring Machines (TBMs) Fast Facts
• Two purpose built, highly specilialised Tunnel Boring Machines (TBMs) imported from Germany will excavate marine intake and outlet tunnels.
• Each $10m TBM weighs 150 tonnes, is 71m long and propelled by hydraulic rams.
• 300-tonne cranes will lower TBMs into the 70m deep intake and access shafts that are used to access the tunnels.
• All TBMs have a round, rotating cutter head on the front face which is covered in disk cutters (like giant teeth). As the head spins, the ‘teeth’ cut into the rock. The rock is crushed and mixed with a naturally occurring lubricant, bentonite clay, to form slurry. It is then pumped via pipelines within the tunnel back to the plant site.
• Each TBM will excavate about 75m of tunnel every week and about 52,000 cubic metres of material will be excavated – equivalent to 50 Olympic-sized pools.
• The TBMs follow a precise route - guided by GPS that follows a survey grid.
• TBMs used because of minimal impact on 1) environment and 2) local community compared to other tunnelling methods i.e. trenching or above ground piping.
• The tunnels will be excavated 70 metres underground (equivalent to a 20-storey building) through solid bedrock.
• Intake tunnel will be 2.2kms long (750m from the plant to the beach at Tugun, then 1.4kms from the beach out to sea, where it will connect to a marine riser, 20 metres below the surface).
• The outlet tunnel will be 2km long (780m from the plant to the beach at Tugun, then 1.2km from the beach out to sea.
• TBMs will not be excavating under any private property as the tunnel route is under public land. It is also highly unlikely that there will be any sound or vibration generated by the TBMs on the surface due to the depth they will be operating
• Six to eight people will be in each TBM at any one time when operational.
• As TBMs excavate, another highly experienced work team will line the tunnels with specially constructed concrete segments. Six segments are slotted together to form a complete ring.
• A total of 21,000 segments will be used to line the two tunnels.
• Tunnels - internal diameter of 2.8m - external diameter of 3.4m with a 0.2m gap between the concrete segments and the tunnel wall. This will be filled with grout.
• At the completion of the project 80% of the TBMs will be recovered from the tunnel shafts.
Thursday, 31 May 2007
Media contact: 3224 4500 (Premier’s office) 3224 4379 (Deputy Premier’s office)